Успешное производство требует больших вложений и постоянного пополнения ресурсов. Без этого Вы не сможете выполнять норму, а это значит, что и не сможете выполнять заказы своих клиентов, что приведёт к самым печальным последствиям. Чтобы такого не случалось, мы рекомендуем Вам регулярно поставлять на свой промышленный объект все необходимые ресурсы в достаточном количестве, чтобы в любой момент Вы могли не только пустить их в серийную работу, но и при необходимости заменить вышедшие из строя детали.
Для того, чтобы добиться такого результата, нужно приобретать детали, особенно те, которые расходуются в достаточно большом количестве, оптом. В покупке оптом есть и другие преимущества кроме запаса тех или иных комплектующих — это более низкая цена по сравнению с розничными или мелкооптовыми поставками, а также особые условия продавцов, как правило, более выгодные для обеих сторон. Наша компания предлагает Вам приобрести пружины оптом — изделия, необходимые на любом производстве. Мы уверены, что в том или ином виде Вы используете пружины в своей сфере, а это значит, что Вам необходим надёжный и проверенный поставщик, готовый выполнить любой Ваш заказ. Если Вы выберете в таком качестве наш завод, то Вы получите верного партнёра и надёжного поставщика.
Оптовые продажи разнообразных пружин
Существует множество видов пружин, и каждый из них востребован на том или ином этапе либо даже направлении производства. Пружину сжатия Москва и многие другие виды этих изделий Вы сможете оптом закупить в нашей компании — мы предложим Вам оптимальные условия на любой Ваш заказ, так как ценим наших клиентов и хотим сотрудничать с ними и в дальнейшем.
Наш завод предлагает приобрести все основные виды пружин — если же Вам нужно что-то более специфическое, то Вы всегда можете обратиться к нашим специалистам, которые помогут Вам решить эту проблему. Итак, у нас заказывают:
- инструментальные пружины — прочные пружины, применяемые для различных прессов, штампов и прочей техники, имеющей аналогичную конструкцию. У нас Вы сможете также заказать пружины сжатия инструментального типа, так как данные категории пружин сходны по функциональности и параметрам;
- пружины сжатия — как уже было сказано, они сходны с инструментальными пружинами, но сжимаются более равномерно, обеспечивая более тугое сжатие и более фиксированное положение. Конические пружины сжатия и другие модификации изделия не деформируются даже при больших нагрузках, они способны выдерживать высокое давление, образуемое при сжатии, и поэтому срок их службы крайне высок;
- волновые и тарельчатые пружины — имеют широкую область распространения, используются в узлах различных агрегатов для создания статической нагрузки.
Производство пружин сжатия и других видов пружин мы вынесли на современный и удобный для покупателя уровень, поэтому будем рады выполнить любой Ваш заказ!
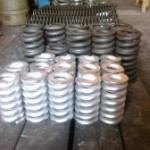
Пружины для грохотов
Пружины для грохотов работают на сжатие и при эксплуатации испытывают большие нагрузки, не требуют специальных покрытий. Пружины для грохотов являются расходным материалом и, в связи с развитием горнодобывающей промышленности и строительства, спрос на них постоянно растет. Наша компания производит пружины для грохотов и дробилок всех типов — пружины для щековых дробилок и пружины для роторных дробилок.
Пружины для грохотов и дробилок производятся из пружинных сталей 65Г, соответствующих ГОСТу 9389-75 и сплавов 70С3А, 65С2ВА, 60С2А, 51ХФА по ГОСТ 14963 и ГОСТ 14959. Диаметр проволоки составляет от 10 до 20 мм.
В связи с тем, что дробильно — сортировочные комплексы эксплуатируются в самых тяжелых условиях, в том числе и зимой, их детали постоянно контактируют с абразивной пылью, испытывают на себе постоянные перепады температур, они часто выходят из строя. Качество пружин, от которых в большей степени зависит бесперебойная работа комплексов, имеет первоочередное значение. При изготовлении пружин для грохотов и дробилок мы используем самые лучшие технологии, вся продукция проходит обязательный контроль качества, а заказы выполняются в максимально сжатые сроки.
Здесь мы подробно опишем процесс очистки и ремонта различных элементов подвижного состава. Листовые рессоры, снятые с вагонов при плановых видах ремонта, очищают от грязи и масла в ваннах, заполненных горячим 3%-ным раствором каустической соды, а затем обмывают чистой водой.
Пружины в депо и на заводах проверяют только по высоте в свободном состоянии. Пружины с изломами или трещинами в витках, протертостями или коррозионными повреждениями более 10% площади сечения прутка бракуют.
Просевшие пружины нагревают в печи до температуры 880—920 °С, подают на станок для восстановления шага между витками и закаливают в масле или воде, подогретых соответственно до 60 или 30—40 °С.
Время от момента извлечения пружины из печи до погружения в закалочную среду не должно превышать 25 с, чтобы металл не охладился ниже 780 °С.
Далее пружины. подают в печь отпуска, где поддерживается температура 440—480 °С. Затем в ванне с водой (или на воздухе) их охлаждают в течение 40—50 мин и подают для испытания и тарировки на прессах.
Пружины, выдержавшие испытание, при необходимости подают на шлифовальный станок для выравнивания опорных поверхностей. Затем производятся приемка и клеймение пружин.
Здесь на пружины с диаметром витка меньше 16 мм навешивают бирки. Отремонтированные пружины окрашивают и сушат.
Для повышения предела выносливости пружин и рессор на некоторых вагоноремонт ных заводах их поверхности упрочняют дробью на дробеметных установках.
Обмытые рессоры осматривают и сортируют по объему ремонта.
Рессоры, признанные годными при наружном осмотре и обмере и не нуждающиеся в разборке, смазывают и подают на гидравлический пресс для испытания на остаточную деформацию под пробной нагрузкой и на действительный прогиб под рабочей статической нагрузкой.
Рессоры, которые необходимо для ремонта разбирать, после устранения неисправностей испытывают. Остаточная деформация не допускается, а прогиб должен быть в пределах нормы согласно техническим условиям по ремонту листовых рессор.
На одну из боковых поверхностей хомута рессоры, выдержавшей испытания, ставят клейма: номер, присвоенный заводу или депо, и дату испытания (год, месяц). После клеймения исправные рессоры окрашивают так же, как новые, складируют на накопительной площадке.
Рессоры, направляемые на разборку, подают к прессу для срезания заклепок наконечников, а затем к прессу для снятия хомутов. Хомут, не поддающийся снятию в холодном состоянии, подогревают со стороны малого листа до температуры 350 «С. После выпрессовки шпильки рессору рассыпают на листы. Листы осматривают, определяют их износ и остаточную деформацию и комплектуют рессору вновь.
Листы рессор, у которых имеются надрывы, трещины, износ или коррозионные повреждения глубиной более 0,5 мм, заменяют. Разрешается наплавлять торец коренного листа эллиптической рессоры грузового вагона при износе не более 3 мм с последующей термообработкой. Взамен забракованных листов подбирают годные, бывшие в употреблении, или изготовляют новые из стали 55С2 или 60С2.
Все деформированные листы рессор подвергают закалке с отпуском. Листы нагревают в печи. Затем осуществляется гибка листов в гибозакалочной машине в течение 25 с (не более) с тем, чтобы- остаточная температура их после гибки была не ниже 780 °С.
Закалка происходит в ванне этой машины, заполненной трансформаторным или веретенным маслом с температурой 60 «С. Разрешается рессорные листы закаливать в воде, подогретой до температуры 30—40^°С, с последующей проверкой магнитопорошковой дефектоскопией с применением сухого порошка на выявление закалочных трещин. После закалки рессорные листы подвергают отпуску, с выдержкой в печи при температуре 440—480 °С в течение 40—50 мин и последующим охлаждением на воздухе. Твердость закаленных, подвергнутых отпуску листов должна быть НВ 363—432.
Сборку смазанных графитной смазкой листов на шпильку, сжатие рессоры, расклепывание шпильки и насадку хомута выполняют на сборочных стендах.
Обжатие нагретого до температуры 900-—! 150 °С хомута производится на специальном прессе таким же усилием, как при изготовлении новых рессор.
Хомуты рессор ремонтируют сваркой при наличии забоин к протертостей на боковых поверхностях и торцах не более 25% площади поперечного сечения. Трещины в хомутах заваривают при условии, если они расположены вне сварных швов и если после разделки иод сварку толщина поперечного сечения уменьшается не более чем на 50%.
Исправные и отремонтированные рессоры после испытания клеймят и окрашивают. Клейма (условный номер, присвоенный заводу или депо, год и месяц испытания) ставят на одну из поверхностей хомута. Окрашивание производят так же, как при изготовлении новых рессор и пружин
Технические требования, правила приемки и методы контроля установлены ГОСТ 16118-70.
Последовательность контрольных операций можно рассмотреть на примере наиболее распространенных.
Внешний осмотр. На поверхности пружин не допускается риски, царапины, следы ржавчины, отслаивание покрытий пользуются специальными реагентами.
Внешний осмотр производят также после термообработки. Для лучшего выявления закалочных рисок, трещин в наиболее ответственных пружинах производят магнитно-порошковую дефектоскопию.
Проверка размеров. Стандарт устанавливает три группы точности пружин:
- первая группа –пружины с допускаемыми отклонениями на контролируемые силы или деформации ± 5% ;
- вторая группа – пружины с допускаемыми отклонениями ± 10% ;
- третья группа – пружины с допускаемыми отклонениями ± 20% ;
В соответствие с группами точности установлены допускаемые отклонения на геометрические параметры: Наружный D (или внутренний D1) диаметр, полное число витков n1, высоту пружины в свободном состоянии H0 и предельно сжатом H3 состояниях, перпендикулярность торцевых плоскостей к образующей пружины и неравномерность шага в свободном состоянии.
Контроль наружного диаметра пружины можно производить универсальными средствами измерения. В этом случае наружный диаметр замеряется не менее чем в трех местах пружины во взаимно перпендикулярных направлениях.
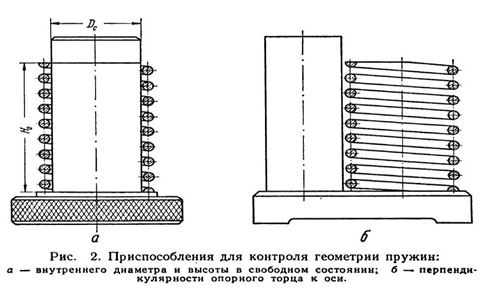
При контроле калибрами длина рабочей части калибра должна быть не менее утроенного шага пружины.
Наружный диаметр пружины в предельно сжатом состоянии проверяют с помощью контрольной гильзы. Помещенная внутрь гильзы пружина сжимается до полного сжатия, до соприкосновения витков, при этом гильза должна свободно перемещаться вдоль пружины. При контроле внутреннего диаметра контрольный стержень должен свободно проходить через полость ненагруженной пружины (рис. 2, а). По контрольным рискам, нанесенным на стержне, производится выбраковка пружин по высоте H0 в свободном состоянии.
Размеры калибров, контрольных гильз и контрольных стрежней должны иметь точность не ниже 5-го класса по ОСТ 1219. В ОСТ 1219 подробно расписаны способы применения калибров и возможные допуска на их отклонение.
Определение числа витков производится путем отсчета целых витков и добавления к ним избыточной доли витка, составляющего часть окружности.
Контроль высоты пружины, сжатой до соприкосновения витков, производится как самостоятельная операция или одновременно с изменением силовых характеристик. За высоту H3 принимается расстояние между опорными плоскостями устройства, сжимающего пружину.
Значения предельных отклонений наружного и внутреннего диаметров, числа витков, высоты пружины и других геометрических параметров приведены в ГОСТ 16118-70.
Проверка перпендикулярности опорной плоскости пружины к ее геометрической оси производится «на просвет» с помощью угольника или вспомогательного цилиндра, ось которого перпендикулярна опорной плоскости (рис. 2, б).
Испытания в статике. Для проверки соответствия характеристики пружины требованиям чертежа к ней прикладывают эталонные нагрузки, измеряя при этом ее длину или деформацию. Такие испытания производят путем постепенного нагружения или разгружения пружины (в зависимости от предъявляемых к ней требований).
Статические испытания производят на универсальных машинах, оборудованных гидравлическим или пневматическим приводом нагружения, а также силоизмерительными узлами и устройствами для измерения деформаций.
В условиях серийного производства мелких пружин целесообразно применять специальные приборы, одна из конструкций которых представлена на (рис. 3).
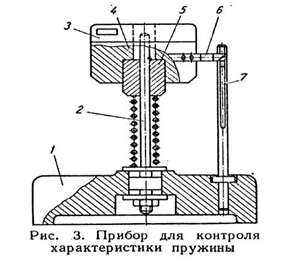
Испытуемая пружина одевается на оправку 2, закрепленную на основании 1. На ту же оправку последовательно насаживаются два груза 3 и 4, причем в груз 4 запрессована направляющая втулка 5. К грузу 4 прикреплен указатель 6, с помощью которого можно отсчитывать показания по шкале (или отдельным рискам) на стойке 7.
В настоящее время созданы универсальные испытательные машины, такие как ИР5040-10П и ИР5047-10П позволяющие определять приложенное усилие и соответствующую деформацию. Эти машины работают на автоматическом режиме нагружения. Их пределы измерения соответственно 0,1-1000 кГ.
В условиях массового производства применяются контрольно-сортировочные автоматы.
К числу статических методов испытания можно отнести и заневоливание. Большая величина остаточной деформации после заневоливания недопустима, какими бы причинами она ни объяснялась: плохой термообработкой, трещинами или другими.
Эффекта, аналогичного заневоливанию, можно добиться так называемой отбивкой — много кратным ударным нагружением на специальных стендах (регламентируется ГОСТ 16118-70), при котором в пружине возникают напряжения, превосходящие предел упругости.
Осадка пружин при этом стабилизируется приблизительно после первых 2000 циклов, а продолжительность испытания сокращается до 2-3 мин.
Динамические испытания. Целью динамических испытаний является определение соответствия качества пружин условиям их эксплуатации при переменных нагрузках.
Если пружины предназначены для работы в условиях ударных нагружений, их испытания производят на копре под ударами свободно падающей бабы. Перед испытанием пружина в специальном приспособлении деформируется на заданную величину предварительного поджима. Вследствие неравномерности распределения напряжений по длине пружины при ударной нагрузке ее следует подвергнуть сериям ударов с обеих сторон.
Пружины, предназначенные для восприятия циклических и многократно переменных нагрузок, подвергаются динамическим испытаниям на специальных стендах. При этом желательно, что бы форма импульса приближалась к эксплуатационной, а максимальные напряжения превышали предел усталости, не достигая, однако, предела упругости данного материала.
Для сокращения общей продолжительности цикла изготовления пружин метод динамических испытаний так же, как и отбивка, может быть рекомендован взамен заневоливания. В этом случае максимальное напряжение должно несколько превышать предел упругости.
Коррозийная защита
В настоящее время для защиты от атмосферной коррозии ряда деталей промышленного производства упругих элементов, используется цинковые и фосфатные покрытия. Для оценки стойкости защитных свойств металлических материалов еще много лет назад ЦНИИ материалов (г.Санкт Петербург) были проведены ускоренные и натуральные коррозийные исследования в промышленной атмосфере, а так же испытания в специальных средах (соляной туман, сернистый газ, пары азотистой кислоты) и субтропическом климате (г.Батуми) с разработкой соответствующих отраслевых стандартов и регламентов, которые внедрены в промышленное производство, оборонной промышленности России (СССР).
Полученные экспериментальные данные позволяют сделать однозначный вывод о том, что в атмосферных условиях цинковые покрытия (в т.ч. в условиях пром-атмосферы) имеют существенные преимущества перед фосфатироваными. При этом было показано, что защитная способность обоих покрытий может быть увеличена практически одинаковыми способами. Для фосфатированых покрытий это применение различных про-кислот (промасливания, пропитка окисляющими растворами и соответствующими лакокрасочными материалами), а для цинковых покрытий – это применение дополнительного фосфатирования с последующей пропиткой аналогичными пропитывающими растворами. Кроме того цинковые покрытия могут использоваться повышенной толщины. Ряд толщин может выглядеть как последовательности чисел 3,6,9 …. 36,42мкм. Фосфатные покрытия (обычные) могут наноситься только одной толщины — около 60-80 мкм. Это объясняет то, что фосфатное покрытие образуется путем химического осаждения на активную железную основу частиц фосфатных солей металлов-железа, цинка, кадмия и как свободная основа заканчивается — покрытие прекращает расти. Цинковое покрытие является электрохимическим и продолжает расти (конечно, до определенного предела) даже тогда, когда имеются уже не железные, а только цинковая поверхность. Следует отметить, что цинковые покрытия по своей природе являются анодными, т.е защищают стальную поверхность электрохимически, как протектор. До тех пор, пока на поверхности имеются частицы металлического цинка, основа детали не разрушается, а разрушается (растворяемая) часть покрытия.
Наглядно это можно представить как заполнение образовавшихся в покрытие пор или дефектных участков продуктами коррозии цинка, которая препятствует взаимодействию агрессивных сред с поверхностью стали.
Фосфатное покрытие является не электропроводимым и больше является похожим на катодное механическое покрытие, которое защищает поверхность самим фактом своего наличия. Там где покрытие повредилось, то тут же начинается коррозия основы.
Защитная способность покрытий в значительной степени зависит от качества сцепления их с основой. Технология нанесения цинкового покрытия на основу включает в себя операцию активирования (т.е спецтравления) и как правило, операцию применения «обратного» тока. Все это приводит к тому, что покрытие осаждается на активную
поверхность стали и активные центры кристаллизации цинка является продолжением кристаллов металла основы т.е.наблюдается непрерывный рост кристаллов металлического материала. (в данном случае сталь-цинк) Кроме того, фосфатное покрытие является хрупким и легко скалывается (проминается), в то время как цинковое покрытие обретает роль твердой смазки и способствует благоприятной работе всего узла при скреплении его.
Учитывая изложенное следует понимать, что применение цинкового покрытия для изделий Вашего предприятия повышает срок их службы по сравнению с фосфатированием и является экономически целесообразным т.к себестоимость изделий при этом не повышается.
Основной причиной залипания сит грохотов является вовсе не качество самого сита, а в принципах функционирования самого грохота. Сито обязательно должно быть закреплено очень жестко, вся нагрузка должна приходиться на пружины для грохота и вибратор. Если это правило соблюдено, то причина кроется в пружине грохота. На грохотах используются цилиндрические витые пружины сжатия. Основная характеристика этих пружин — уменьшение длины при нагрузке. Когда пружина сжатия не подвергается нагрузкам, ее витки не касаются друг друга. Пружины грохота устанавливаются на его короб и находятся под постоянной нагрузкой. При работе они преобразуют деформацию сжатия в деформацию кручения пружинной стали, из которой она изготовлена.
Если пружина грохота на 10 — 20 мм проседает, это отрицательно сказывается на уменьшении колебаний при грохочении, хотя и не заметно «на глаз». Проседание пружины грохота и является главной причиной залипания. При обслуживании сортировочных участков зачастую не отслеживают состояние пружин, что негативно сказывается на всем процессе производства. Менять пружины грохотов рекомендуется раз в 1 -2 года.
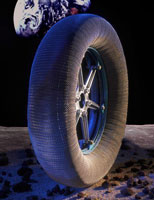
Лунная шина
В результате сотрудничества NASA и компании Goodyear была создана специальная шина, которая может быть использована в больших транспортных средствах, передвигающихся на дальние расстояния, на Луне. Данная шина не нуждается в использовании в ней каких либо газов. Так называемая «пружинная шина» состоит из 800 металлических пружин, выступающих в роли несущей конструкции, и способны выдерживать длительные большие нагрузки. По своим характеристикам эти шины значительно превосходят проволочную сетку, которая использовалась в шинах лунохода Apollo. Разработчики говорят, что эта шина значительно упростит исследование нашего спутника в будущем.
Как говорит руководитель исследовательского центра NASA (Кливленд, США) Виваке Аснани, данный проект был реализован потому, что агентству требовались устойчивость и грузоподъемность шин для лунных аппаратов. В первую очередь специалисты пересмотрели дизайн старой лунной шиноы. Решение было простое и эффективное. Сотрудники NASA и Goodyear применили сетку из способных выдерживать большие нагрузки пружин. Впервые «пружинные шины» применили на луноходе Electric Rover и тестовом транспорте NASA. Затем разработка прошла успешные испытания на полигоне Джонсоновского Космического Центра «Рок Ярд».
Руководитель исследований, представляющий в проекте Goodyear, Джим Бенцинг заметил, что новые шины для луноходов оказались очень прочными и экономичными. Конструкция этих шин создает необходимое сцепление за счет того, что пружины позволяют прижиматься к поверхности. Энергия же, которая образуется при сжатии пружин, возвращается, как только контакт с поверхностью прекращается. К тому же эта шина не нагревается при трении.
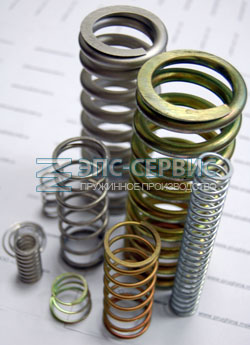
Винтовые пружины
Винтовые пружины изготавливаются из проволоки. Отличительной особенностью этих изделий является то, что под действием внешних нагрузок они изменяют вои геометрические параметры. Таким образом, в винтовых пружинах происходит накапливание энергии. Применяется это их свойство и в машиностроении, в автомобильной, медицинской и сельскохозяйственной технике. Винтовые пружины являются основным элементом амортизаторов, возвратных механизмов, регуляторов расходов топлива.
В целом выделяются следующие типы винтовых пружин: цилиндрические, конические и мини-блоки. На винтовые цилиндрические пружины распространяется ГОСТ 13764-86. Этот нормативный документ определяет качество пружин, изготовленных из стали круглого сечения, которые предназначены для эксплуатации при температурном диапазоне от -60 до +120 градусов Цельсия. Помимо классификации по типу, винтовые пружины делятся на классы, разряды и виды. В зависимости от того, к какому классу принадлежит изделие, определяются и требования к технологии изготовления. Так же это определяет выбор используемых материалов, потому что необходимо учитывать режим их нагружения и выносливости.
Для пружин растяжения с предварительным напряжением допускается применение ГОСТов 13766, 13767, 13770, 13771 к основным параметрам витков.
Цилиндрические пружины подразделяются на 3 класса. К первому классу относятся изделия, которые испытывают циклические периоды растяжения и сжатия. Второй класс винтовых цилиндрических пружин помимо циклического растяжения и сжатия способен устойчиво выдерживать еще и статическое нагружение. К третьему классу винтовых пружин относятся пружины сжатия циклического нагружения с возможностью инерционного соударения витков. Характеристики изготовления всех этих классов четко регламентированы упомянутым выше ГОСТом. К пружинам растяжения с предварительным напряжением помимо основных параметров витков применяются еще и следующие нормативные документы: ГОСТ 13766, ГОСТ 13767, ГОСТ 13770, ГОСТ 13771. Они регламентируют уже не материалы и технологии, а возможные отклонения и допуски. Если более точно, то приведенные ГОСТы устанавливают геометрические и силовые характеристики пружин. Здесь же приведены сведения о том, какое покрытие следует использовать в том или ином случае. Это может быт защитное порошковое покрытие из полимерных материалов или гальваническая обработка поверхности пружин: химическое фосфатирование, цинкование, химическое оксидирование. Текстом нормативных документов предписано проводить лабораторные испытания, в которых прописано правильное поведение винтовых пружин соответствующего класса. Можно видеть, что к данному виду изделий предъявляются высокие требования. Компания ООО «ЭПС-Сервис» гарантирует соответствие винтовых цилиндрических пружин всем указанным нормативным документам.