Изготовление пружин
- Навивка пружин на автомате
- Торцовка (шлифовка торцов)
- Термообработка пружин (закалка в масле, отпуск)
- Обжатие (зеневолевание) пружин
- Пескоструйная обработка (в соответствие с ГОСТ 16118-70)
- Гальванирование
- Выходной контроль продукции, сдача на склад
Изготовление пружин
Поиск потребителей пружин начинается с определения той отрасли, в которой востребована продукция такого типа. Далее необходимо произвести поиск конкретных организаций с учетом их территориального размещения.
Каждый отдельный менеджер получает для дальнейшей работы регион, в рамках которого он и осуществляет свою деятельность по поиску потенциальных клиентов. После сбора общей информации о производственных предприятиях и торгово-промышленных компаниях, которым может понадобиться изготовление пружин он связывается с ними с целью установления контакта и выяснения дополнительных подробностей, которые помогут в будущем.
Алгоритм работы заключается в следующих действиях:
- Поиск контактных данных в сети Интернет тех служб организации, которые представляют интерес (официальный сайт).
- Определения списка тех лиц, которые отвечают непосредственно за формирование заказа при покупке пружин для нужд предприятия.
- Установление контакта с таким лицом. Менеджер должен расположить его к конструктивному общению, после чего сообщить ему об имеющихся возможностях по поставкам пружин, ассортименте этой продукции, преимуществах в сравнении с конкурентами (как технических характеристик изделий, так и организации торгового процесса).
- Получение от заказчика конкретного задания, в котором изложены все его требования.
- Подготовка и передача заказчику коммерческого предложения, созданного на основе его задания.
Расчет пружин производится в техническом отделе. При поступлении такой заявки технологи проверяют чертежи и прилагающиеся к ним документы. В них должны быть указаны следующие параметры:- геометрические размеры пружин;- силовые диаграммы пружин (сжатия, растяжения);
- предельные нагрузки изделий.
Специалисты отдела оценивают сложность изготовления пружин, с учетом имеющегося на предприятии оборудования. Они создают и отмечают в своем отчете список той оснастки, которая может потребоваться для выполнения технологического процесса в соответствии с ГОСТом. Если возникли затруднения, то на этом этапе можно провести переговоры с заказчиком для внесения соответствующих корректировок.
Далее проект будущей работы поступаетв коммерческий отдел, в котором происходит формирование цены за единицу продукции.После того, как менеджер получит такой расчет стоимости, он начинает подготовку коммерческого предложения для заказчика. В этом документе должны присутствовать следующие данные:
- полное наименование организации, заказчика продукции;
- наименование чертежа (пружины);
- количество изделий (в штуках);- стоимость пружин с учетом НДС в расчете на одну единицу;
- срок изготовления заказанной партии товара;
- способы оплаты;
- варианты доставки груза покупателю.
В коммерческом предложении допустимо размещение дополнительных вопросов, которые не были решены в ходе предварительных переговоров, но требуют точного определения до момента начала работы над поступившим заказом.После того, как все формальности будут соблюдены, и заказчик подтвердит свое желание об изготовлении данной партии изделий, ему выставляется к оплате соответствующий счет.
После поступления денег на расчетный счет предприятия, заявка, созданная в программе УНФ, получает статус «В работе» и на нее составляется маршрутный лист. Этот документ будет необходим для производства, так как именно он сопровождает изготовление оплаченных заказчиком изделий. Чтобы не было путаницы при выполнении различных заявок, маршрутному листу присваивается уникальный номер. Наличие такой метки позволяет отслеживать ход производственного процесса с помощью программы УНФ 1С, причем это будет возможно сделать на каждом этапе создания пружин. Упомянутый выше маршрутный лист служит основанием для получения сырья со склада, соответствующего техническому заданию, полученному от заказчика. Надо подчеркнуть, что все материалы, поступающие на предприятие контролируются с помощью химического анализа на соответствие определенному ГОСту.
На начальном этапе, при поступлении на производство, все сырье проходит тщательный химический анализ на соответствие ГОСТам.
Навивка пружин на автомате
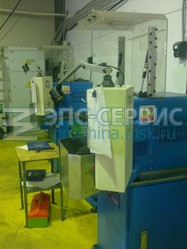
Навивка пружин
Навивка пружин представляет собой технологическую операцию, во время кот
орой заготовка (лента или проволока) изгибаются в плоскую, цилиндрическую или коническую форму. Навивка может быть холодной и горячей. Холодная навивка осуществляется при диаметре проволоки 0,2 — 14 мм, а горячая — от 14 до 60 мм.Навивка цилиндрических пружин осуществляется несколькими способами:
- при помощи двух упорных штифтов и двух
- подающих роликов (холодная навивка);
- при помощи подающих роликов и упорного штифта, который перегибает проволоку через неподвижную оправку (холодная навивка);
- при помощи навивания на вращающуюся оправку (как холодная, так и горячая навивка).
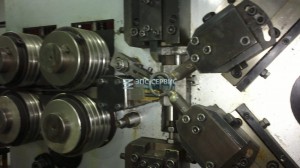
Изготовление пружин 1
Навивка фигурных пружин (конических и т. п.) чаще всего осуществляется на специальных полуавтоматических оправках и приспособлениях.При навивке пружин из проволоки диаметром от 50 мм вместо штифтов на станки устанавливаются прочные упорные ролики с прорезанными в них канавками.
Конические пружины изготавливают методом смещения штифтов к исходной точке во время навивки.
Пружины растяжения получаются при смещении наружного штифта или ролика вперед под прямым углом к плоскости навивки.Горячая навивка пружин осуществляется на полуавтоматических станках. Схема навивки располагается на оправке.
Отрезка готовых пружин осуществляется наружным или внутренним (в зависимости от навивочного станка) во время остановки подачи.
Торцовка (шлифовка торцов)
После навивки пружины, в случае необходимости, подвергаются механической обработке. У пружин растяжения и кручения формируют технологические зацепы и концы. Излишки обрубаются с помощью специальной оснастки и инструмента.
Пружины сжатия, в свою очередь, торцуются на специальных торцешлифовальных станках в соответствии с требованиями. Так же для обработки торцов пружин сжатия применяют точила с абразивными кругами.
Термообработка пружин (закалка в масле, отпуск)
Термообработка готовых изделий позволяет придать им необходимые механические и физические свойства. Различают три основных типа термической обработки пружин: отжиг, закалка, отпуск, нормализация и старение.
Отжиг применяется для улучшения обрабатываемости изделия и в качестве подготовке к последующей термической обработке. При отжиге изделие нагревают до определенной температуры, выдерживают при ней некоторое время и затем медленно охлаждают.
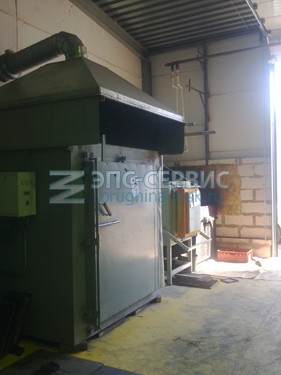
Термообработка
Закалка применяется для получения пружины с повышенной износостойкостью, прочностью и твердостью. При закалке готовые пружины нагреваются до необходимой температуры, затем быстро охлаждаются в воде.
Отпуск позволяет изделию уменьшить внутренние напряжения и повысить вязкость стали, при этом сталь не теряет своей упругости и прочности. При отпуске изделия нагревают после закалки, выдерживают при заданной температуре, а затем охлаждают.
Во время нормализации повышаются механические свойства, уменьшаются внутренние напряжения и улучшается сама структура стали. При этом изделие нагревается выше температуры превращений, выдерживается и затем охлаждается на воздухе.
Старение способствует стабилизации свойств и размеров изделия. Таким образом удется добиться более долгого срока службы пружины.
Обжатие (зеневолевание) пружин
Обжатие пружин — это процесс технологического упрочнения пружин. Данной процедуре подвергаются все типы пружин, изготовленные из проволоки сечением более 12 мм. Обжатие осуществляется после прохождения изделием термической обработки.
Пескоструйная обработка (в соответствие с ГОСТ 16118-70)
Пескоструйная обработка изделий является ключевым технологическим процессом при нанесении различного рода защитных покрытий. Благодаря тому, что данная обработка позволяет практически идеально очистить поверхности, покрытия плотно ложатся на изделие, долго не истираются, соответственно, продлевается срок службы и самой пружины.
Гальванирование
Гальванирование — это нанесение на пружины различных типов покрытий. В зависимости от технологических требований и условий эксплуатации, гальваника наносится разная. Виды нанесения гальванических покрытий: кадмирование, хромирование, полимерно-порошковое покрытие, электрополирование, химическое фосфатирование с промасливанием, оцинкование.
Выходной контроль продукции, сдача на склад
Конечным этапом производства является выходной контроль качества продукции и ее сдача на склад. Выходной контроль представляет из себя проверку химического состава изделий на соответствие ГОСТам, испытания физических и механических свойств и проверку на соответствие чертежам и требованиям заказчика.